Businesses are using data-driven strategies more than ever. This often involves utilizing artificial intelligence algorithms, even for industrial applications. As a result, people are starting to talk about AIoT, to refer to intelligent IoT technologies that incorporate AI.
So, how do artificial intelligence algorithms work, and how can they be used for industrial applications? For example, how can models be trained to support data mining and processing in Industry 4.0?
By enabling AI algorithms on the edge of field devices, the process of generating insights and optimizing production becomes simpler and more efficient.
The starting point is to choose an application and a purpose for our model: for example, the implementation of IoT technologies, and then start with generating a solid database on which to train a model.
Let’s see how to do this with the Zerynth Industrial IoT & AI Platform!
Intelligent and thinking machines
Today, there is a lot of discussion about generative artificial intelligence. However, as far back as 1950, Alan Turing, considered the father of artificial intelligence, posed the question “Can machines think?”
Today, we have a clearer answer to this question.
Consider Google Maps, Amazon’s shopping recommendations, social network sponsorships, or voice assistants. The answer can only be yes.
However, we often see the failure of many algorithms that cannot learn from the world around them.
This happens because one focuses on the medium rather than the problem to solve. Whenever one wants to use an artificial intelligence algorithm, especially in industry, the fundamental questions to ask are: when and why?
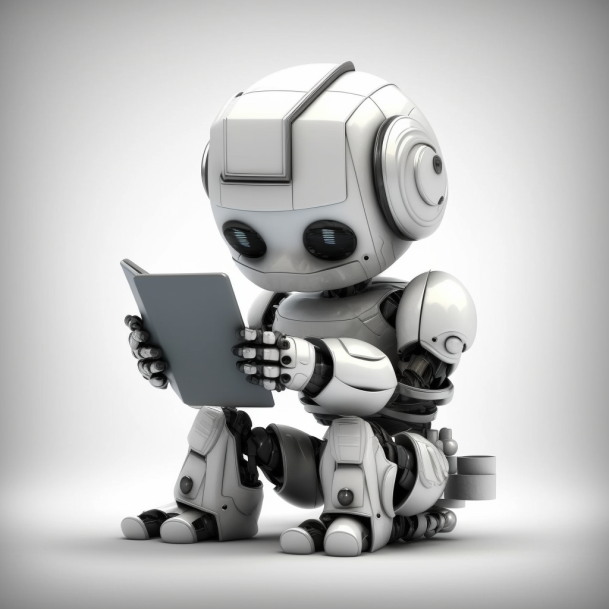
AI generated image based on a text prompt
Artificial intelligence: when and why
When?
The answer relates to the temporal context in which the project takes place; to date, the total digitization of assets is still a distant goal, and assuming algorithms without a data history is very difficult, if not impossible.
Why?
In this case, broader reasoning is required, which presupposes, first of all, knowing what artificial intelligence techniques are.
A definition of Artificial Intelligence
Marco Somalvico, an Italian academic and specialist in the field of artificial intelligence, gave this definition:
“Artificial intelligence is a discipline belonging to computer science that studies the theoretical foundations, methodologies, and techniques that enable the design of hardware systems and systems of software programs capable of providing the computer with performance that, to a common observer, would appear to be the exclusive domain of human intelligence.”
The key words in this definition are “…would seem to be of exclusive relevance to human intelligence”: just like human beings, machines require training. But then, what happens when artificial intelligence is used for industrial applications?
Artificial intelligence in Industry 4.0
For machines to learn to recognize valuable data and to respond in a human-like manner, they require access to large amounts of data.
While humans use machines to carry out mundane, and above all, repetitive work, it is precisely because machines are designed for this purpose.
A repetitive process does not require any intelligence, so it becomes useless to teach a machine what it is already programmed to do; instead, it becomes vital to make an asset recognize certain conditions, a consequence of the data it uses, to provide insight to humans.
In this way, a link is created between the data produced and the information that humans can understand. This way, the decisions are data-driven, and the know-how is digitized systematically.
Having clarified these assumptions, we can understand why artificial intelligence techniques are used: to address a known problem for which there is no apparent solution using data analysis.
All successful AI stories have these factors in common: solving a specific problem with a quick and easy solution and having a large amount of previously recorded data.
AIoT: Intelligence on the Edge
As technology advances, it becomes easier and easier to generate data from assets and interconnect them on a standard network. These two factors result in the exponential growth of traffic that could lead to the collapse of corporate networks.
For this reason, the decentralization of intelligence is of strategic and functional importance for an IoT project.
IoT technologies are considered enabling technologies supported by artificial intelligence. Indeed, the enormous amount of data generated by connected devices, if properly analyzed, makes it possible to create advanced algorithms and specific models.
The architecture of an Artificial Intelligence project
But what does it mean to undertake an artificial intelligence (AI) project? To train a continuous learning algorithm, starting from a solid and structured database is essential. How does my machine behave? What recurring actions can be schematized into ‘rules’ of behavior?
Machine operation data is taken as input to create a new operating model. Then, the hypothesis is tested on the part of the data through statistical prediction or inference. The process is divided into two parts: training the algorithm on a data set (training and validation process) and testing the model on new data (testing process).
Fig. How a continuous learning model works
This second step ends with the calculation of the prediction error, verification of the observed demand, and final feedback on the performance of the created model.
The new model is always in continuous learning: it never stops learning from the data generated. In this way, it constantly improves its performance as the machine works.
Zerynth and artificial intelligence on the Edge for industrial applications
More companies still need to be fully aware of the benefits that comprehensive digitization processes can bring to production. And even fewer know the benefits of using AI and IoT technologies.
Why extract data from your machinery? Understanding the functioning to create a process history allows one to carry out precise data analyses and arrive at unexpected conclusions about the functioning of one’s machines.
Over time, extracting data from devices makes it possible to create a history of production processes and, subsequently, even train sophisticated artificial intelligence algorithms for industrial applications.
The monitoring of machine parameters (e.g., temperatures of use, current draw, etc.) makes it possible to fully understand the work process, make it smoother, avoid machine downtimes or problems during work phases, up to the creation of artificial intelligence algorithms capable of supporting the decisions and strategies of one’s own company.
If you want to learn more, read how Artificial Intelligence (AI) algorithms and machine learning enable companies to adopt predictive maintenance techniques, embarking on a complete digitization 4.0 journey.
Share This Story, Choose Your Platform!
Follow Zerynth on
Latest Posts